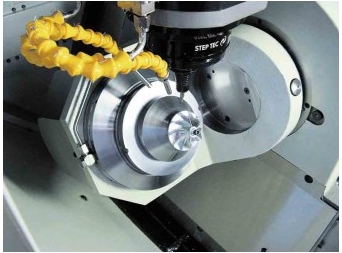
We can easily find that a large amount of resources are consumed; oil production cannot keep up with the needs of developing countries such as China and India; air pollution caused by exhaust gas and smoke and dust emissions; pollution of rivers, lakes and seas caused by the discharge of waste water and harmful substances; Temperance in urbanization, destruction of the ecological environment caused by farmland occupation, deforestation, etc., and rising labor costs are all reasons for the outbreak of the third industrial revolution.
The impact of the third industrial revolution on machine tool manufacturing technology was affected by the third industrial revolution. Machine tool manufacturing technologies have successively focused on energy-saving, environmental protection, and green development. High-efficiency, high-speed, high-precision, etc. have always been the machine tool industry. the goal that is pursued. The collection of these essences is a prelude to the revolution in machine tools. We may wish to concentrate on these results.
Machine structure innovation The invention of parallel machine tools At the end of the last century, G&L Corporation of America unveiled the prototype of a parallel machine tool at the International Machine Tool Show in Chicago. It is a six-legged measuring platform, from which the machine moves from the traditional C-type transmission chain structure to parallel movement. Development has become a trend.
The so-called parallel machine tool is based on the spatial parallel mechanism. It replaces part of the hardware with numerical control software, replaces some of the mechanical devices with electronic devices and components, and quickly realizes the relative position between the tool and the workpiece by changing the length of the truss rod and moving the position of the fulcrum. Position changes, thus breaking the traditional kinematics principle of the machine based on the rectangular coordinate system.
Parallel machine tools are developing toward series-parallel connection because of their weak points such as poor rigidity. China Tsinghua University, Harbin Institute, Long March Machine Tool and other units have taken an international leading position in R&D.
The invention of inverted vertical lathe The German inverted vertical lathe, invented by EMAG, is particularly suitable for the mass production of lightweight rotary components. Immediately afterwards, novel machines such as inverted machining centers, inverted composite machining centers and inverted welding machine tools emerged.
The innovative composite processing machine tool and technology of the processing technology is undoubtedly the lucky star of the large-scale workpiece processing manufacturer. This is because the integration of the process makes the idle time in the middle of the workpiece much less, so the beat time in the whole production process can be compared with the traditional equipment. Significantly shortened; can save the purchase of fixed assets for multiple machine tools; reduce the use of warehouse area, reduce storage costs; shorten the time for replacement.
In the mid-1990s, Austrian WFL invented the turning and milling complex machining center. The Japanese MAZAK company believes that DoneInOne is the direction of the development of CNC machine tools, that is, can complete all the processes in a machine tool.
Laser Processing Along with the continuous development of laser cutting and laser forming technology, DMG's DML40SL can directly input CAD drawings. Three linear axes, two deflection mirrors and one focus axis. The laser beam enters the surface of the workpiece in an angle range of less than 200 to be processed.
The laser pulse method YAG, laser power 100W, laser beam diameter Φ0.04 ~ 0.1mm, metal removal rate of 25mm3/min.
Ultrasonic vibration processing Special milling cutters, drill bits or grinding wheels made of industrial diamond particles are used to perform high-precision machining of superhard materials through high-frequency percussion of 20,000 vibrations/s.
The spindle speed of the machine tool is 6,000r/min, the drive power is 10kW, and the spindle high-frequency vibration power is 1.5kW.
A water-jet waterjet is used to press normal water through an ultra-high pressure pressurizer to a pressure of 380 MPa (55,000 psi) or higher and then through a fine nozzle (its diameter is Φ0.01-Φ0.04 mm). A water arrow with a speed of 915m/s (about 3 times the speed of sound) cuts. Waterjets are divided into two types: waterjets and waterjets.
Flexible Manufacturing (FMS)
The analysis of the FMS should focus on the master control system, the transport trolley, the exchange tray warehouse, and the washing machine. The machine tool (mainly lying) is only one of the units for machining parts. Because of the FMS developed and developed by robotics, the main function is not only to test the adaptive capacity of the processing unit, but also to take care of the ability of moving objects around the workstation and the ability to respond to remote sensing data.
Smart manufacturing intelligence is one of the important components of advanced manufacturing technology. It integrates information technology, optoelectronic technology, communications technology, and sensor technology to promote the continuous progress of machine tool manufacturing. Japanese companies such as MAZAK and OKUMA have obtained a number of patents for R&D in this area. As a system supplier, German HEIDENHAIN in their software has integrated adaptive feed control (AFC: Adaptive Feed Control), automatic calibration and optimization of machine precision (KinematicOpt) and intelligent chatter control (ACC: ActiveChatterControl), etc. For the user to choose.
Today's high-end machine tools are generally equipped with thermal deformation control systems to ensure the stability of the machine's working accuracy. Like Japan's Yasuda Corporation, they have developed a high-precision horizontal coordinate machining center with a "body temperature control device." As for the anti-collision function, it is ever-changing and endless.
The GF AgieCharmilles Group's smart processing in Switzerland is all about improving the technological level. Their Mikron series intelligent machining modules can help users control the milling process for higher performance, higher quality and safety.
Micronano Manufacture Shanghai Machine Tool Works Co., Ltd. independently developed nano-grinding machine, mainly used in nano-precision grinding of micro-electromechanical optical components such as superhard brittle, super-hard alloy, die steel, electroless nickel plating and other materials. Processing range: non-spherical surface diameter <φ10mm, positioning accuracy ≦ 0.1μm (100nm), repeatability positioning accuracy ≦0.05μm (50nm), surface roughness Ra<0.01μm (10nm), online measurement compensation processing, grinding wheel dressing And online trimming features.
Two revolutionary measures 3D printing 3D printing came into being in the third industrial revolution. It is a new manufacturing method of manufacturing. Additive manufacturing can produce high-precision, complex surface metal and non-metal parts. This kind of precision machining method can avoid the interference of the tool and can process the irradiated part where the laser beam is blocked.
There are many kinds of 3D printing technology. There are several methods, such as laser powder molding method, molten plastic molding method, and photosensitive resin molding method. The principle of technology is that no matter what kind of molding method, 3D objects are formed by adding raw materials and layers, each time printing. One layer of material is only 0.1-0.2mm thick. Compared with two-dimensional printers, 3D printers have one-dimensional, that is, Z-axis, through the XYZ axis of movement, the raw materials layer by layer, such as molten plastic molding, nozzle spray Out of the molten plastic wire, the platform for the three-dimensional motion, you can build a 3D physical (equivalent to a layer of glue up).
Liquid nitrogen cryo processing MAG has developed a set of cutting cooling system that subverts traditional methods - "ultra-low temperature liquid nitrogen cooling cutting technology", which has become a revolutionary innovation in the machine tool industry. Mr. Li Li, President of MAG Asia Pacific, stated that “the promotion of this technology will have a revolutionary impact on the machine tool and tool industry. High efficiency and long life will reduce the consumption of machine tools and tools, while reducing the consumption of earth resourcesâ€.
The cutting heat in the cutting process results in rapid wear of the tool when machining the superhard material, a large tool consumption, and the tool cost even exceeds the cost of the machine tool. The introduction of ultra-low temperature liquid nitrogen cooling cutting technology can achieve liquid nitrogen in the micro-holes of the blade cutting edge through the center of the spindle and the center of the tool shank. The heat generated by the cutting tool is vaporized by liquid nitrogen (the boiling point of liquid nitrogen is -320°C. The instant take away, especially in superhard material processing and composite material processing will have better results, cutting speed can be greatly improved, and tool life can be greatly extended.
According to MAG's cutting test statistics over the past few years, when machining difficult-to-cut materials such as titanium, nickel-base alloys, spheroidal graphite cast iron, or vermicular graphite iron, the metal removal rate can be increased by an average of 3 times, and the tool life can be extended by an average of 2 times. This means that a single machine tool can be used as three machine tools, and one blade can be used as two blades, which greatly saves the use of equipment, space, personnel, and tool and energy consumption.
The technology is environmentally friendly. Usually, the means of metal cutting cooling is the use of coolant or cooling oil, and the coolant or cooling oil not only pollutes the environment and needs recycling, and the oil mist treatment is not good or even unsafe due to flaming and burning. Nitrogen is a safety gas and natural emission. There is no pollution in the air and no recycling is required.
Future Machine Tool Prospects Concealing Winding Machine Parts for carbon fiber and other materials can be processed by winding.
The orbital milling grinding machine may also be a moving train. The front wheel is a milling cutter disk, and the damaged track is flattened; the rear wheel is a grinding wheel and polishes the flattened track.
Otsuka slogan and MAZAK model Japan Otsuka proposes that the direction of future machine tool development should be: SPACECENTER has features such as SPEED, POWER, ACCURACY, COMMUNICATION, and ECOLOGY.
The MAZAK establishes the future machine tool model: spindle speed 100,000r/min, acceleration 8g, cutting speed 2 Mach, synchronous tool change, dry cutting, collecting, milling, laser machining, grinding, and measuring.
The Yangtze River is not rolling and the waves will always push forward. The advanced manufacturing technology in the third industrial revolution period, its development speed, and its change cycle will be faster than any period in history. Therefore, the development of CNC machine tools in the new era will make us dizzying and promote social development. The constant progress.
Combining the characteristics of investment in mainland China, a fine processing plan for apricot, plum and peach processing production lines has been formed. According to the investment status and production reality of the enterprise, the customer's engineering project can be designed on a case-by-case basis, and then handed over to the customer as a real turnkey project. We are committed to developing innovative equipment to improve overall operational efficiency and significantly reduce capital investment.
It is suitable for the processing of apricots, plums, peaches and other stone fruits, and can produce clear juice, cloudy juice, puree, concentrated juice, concentrated pulp, fruit powder, fruit vinegar and other products. The production line is mainly composed of washing machine, elevator, ultraviolet sterilizer, denuclearizer, beater, degasser, homogenizer, sterilizer and filling machine. The design concept of this production line is advanced and the degree of automation is high; the main equipment is all made of high-quality stainless steel, which fully meets the hygienic requirements of food processing.
Fruits Jam Machinery,Fruits Jam Machinery Mango Jam Making Machine,Fruits Jam Machinery Pineapple Jam Making Machine,Fruits Jam Machinery Blueberry Jam Jam Machine
Jump Machinery (Shanghai) Limited , https://www.shanghaimachineries.com