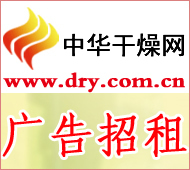
At the annual meeting of the Methanol Industry Gas Purification Technology Exchange, we learned that China's synthetic ammonia technology is being transferred to the localization, large-scale, low-pressure, cleanliness, and high-efficiency “five†directions. Yangmei Zhengyuan, Xinlianxin, Luxi Chemical Such companies as Shanxi Tianze, Yangmei Fengxi, Hunan Anxi, and Nanjing Guochang have conducted beneficial explorations. Experts predict that during the "Twelfth Five-Year Plan" period, this transfer will lead China's nitrogen fertilizer industry to a new height.
Yu Zifang, a well-known expert in the domestic nitrogen fertilizer industry engaged in nitrogen fertilizer design, production, and research for 40 years, pointed out in an interview with reporters that ammonia synthesis towers and systems are the last link in the industrial ammonia production and are the most important and complex devices. First, the selection of the system device and process technology directly affects the level of energy consumption. Can the weapon of the country control the hands of others? Therefore, the importance of domestically produced ammonia technology devices is self-evident.
In October 2011, Luxi Chemical's 360,000-ton/year synthetic ammonia plant, a large-scale synthetic ammonia project using domestically-made ammonia synthesis towers and triple-tube direct waste boilers and other new low-pressure synthesis technologies, was successfully launched and put into production once. This is the first large-scale low-pressure ammonia synthesis plant that completely adopts China's independent intellectual property rights. The system pressure, tower pressure difference, plane temperature difference, ammonia net value, system resistance and other indicators are all ideal, which lays a solid foundation for further optimization of large domestically produced low pressure ammonia synthesis process. The successful launch of the device means that China has fully mastered the complete set of independent technologies for large-scale low-pressure ammonia synthesis projects and ended the long-term dependence of key technologies for low-pressure ammonia synthesis on foreign countries. Domestic equipment and technology broke the long-term monopoly of the two top companies in Denmark, Topsoe and Casale in Switzerland, and formed a competitive and competitive situation with international giants. The cost of building an equivalent device will be 30. The reduction of RMB 100 million to RMB 1.8 billion will not only significantly reduce construction costs, but will also strongly promote the progress and development of the domestic ammonia industry.
At the same time, for large and powerful companies, large-scale installations can take advantage of large-scale production, not only representing a high degree of technology, but also implying an increase in efficiency. Yang Chunsheng, chairman of the Shandong Chemical Fertilizer Industry Association, said that during the “Twelfth Five-Year Plan†period, the production capacity of Hunan Anxi IIIJD4000 ammonia will be increased to 300,000 tons per year. Guochang’s domestic technology is expected to increase the single ammonia plant to 450,000 tons. The scale of annual production of 600,000 tons/year; and the chemical fertilizer of Zhangzhou Zhengyuan can also reach the scale of 600,000 tons/year of synthetic ammonia. If these ideas can all be implemented, it will undoubtedly lead China's nitrogen fertilizer industry to a new height.
As a witness to the development of the nitrogen fertilizer industry in China, Yu Zifang pointed out that low pressure is also the current development trend of ammonia synthesis technology. He said: "The development of synthetic ammonia in our country has experienced a process from low pressure to medium pressure to high pressure. The earliest implementation of the new China was 12.5 MPa, followed by 15 MPa and 20 MPa. "From the viewpoint of energy saving, environmental protection, and efficiency improvement, based on the study of advanced technologies for ammonia synthesis abroad, China's ammonia pressure has dropped from a high pressure of 32 megapascals (now 32 megapascals is already relatively small) to a drop of 25 trillion." Pa, many domestic scientific and technological units have developed and innovated a variety of low-pressure ammonia synthesis technology. Some large-scale devices have reached 22 megapascals and 20 megapascals, and some large-scale devices have now reached 15 megapascals and have achieved very good results. Less than 20 MPa low-pressure synthesis technology has been applied in Zhengyang Zhengyuan, Henan Xinlianxin, Luxi Chemical and other enterprises, with obvious energy and economic benefits, which has laid a good foundation for the domestic production of large-scale ammonia synthesis technology and equipment in China. It is understood that the existing 15 megapascal system that has been operating by car includes Shandong Hongda 150,000 tons/year ammonia synthesis system, Xinjiang Hongji Coking 120,000 tons/year ammonia synthesis system, and Sichuan Jinxiang Chemicals 240,000 tons/year ammonia. The synthetic system and Anhui Zhongneng (Linquan) 300,000 tons/year ammonia synthesis system have obvious development trend of low pressure.
If large-scale production represents an increase in production efficiency, cleanliness and high efficiency reflect the increase in the quality of production processes, which is also a requirement for sustainable development. Shijiazhuang Zhengyuan is a typical example of practicing "five changes". At the end of last year, the company's annual output of 240,000 tons of synthetic ammonia and 400,000 tons of urea project, the main equipment of the synthesis system (including internal parts) have achieved localization; the synthesis of the tower from three sets of 1000 expanded to the JR type DN2400, fresh gas methane The content decreased from 3.4% to 2.3%, and the normal operating pressure for synthesis decreased from 25.4 MPa to 17.0 MPa; the new system saved 0.059 tons/ton of ammonia, saved 118.67 kWh/ton of ammonia, and produced 0.356 tons of steam. Tons of ammonia, the annual added benefit of 34,596,200 yuan, the synthetic system investment can be recycled within two years, "five" transfer benefit is very obvious. According to reports, Zhengzhou Zhengzhou Fertilizer's annual output of 600,000 tons of synthetic ammonia and 800,000 tons of urea project also plans to adopt this technology. In addition, the domestically produced IIIJD3500 ammonia synthesis system used by Henan Xinlianxin has a fresh gas methane content of 1.56%, a synthetic normal operating pressure of 17.0 to 18.0 MPa, an ammonia production of 900 to 922 ton/day, a byproduct of 2.73 MPa, steam at 321°C. , After the production effect is remarkable.
It is understood that in accordance with the direction of "five changes," Hunan Anxie has an annual output of 300,000 tons of ammonia, which is larger (nominal diameter DN2700, DN3000, etc.) The domestic ammonia synthesis system is in the design and development stage, and the indicators will be further optimized. . The fresh gas methane content of the IIIJD4000 (DN2700) unit is almost zero, the ammonia content in the tower is 2.3%, the ammonia content in the tower is 20.27%, the pressure is ≤15 MPa, the tower resistance is 0.25 MPa, and the system pressure difference is about 0.9 MPa; It will also produce 3.9 MPa of 420°C superheated steam at 59 tons per hour. It will be used to drive condensing turbines with a steam consumption of 5 kilograms per kilowatt and an hourly capacity of 11,800 kilowatts, saving electricity compared to 190 kwh per ton of ammonia. , Energy-saving effect is obvious.
This product [100t Cement Silos" is adopt split cement silo is connected to the cylinder wall by bolt sealing strips, and the top of the silo is equipped with a pressure safety valve to balance the pressure in the silo. Prevent explosions. Each cement silo is provided with an upper and lower material level indicator, which can display the empty state of the silo.
100Ton Bolted Cement Silo,100Ton Cement Silo,Construction Cement Silo,100T Concrete Cement Silo
Shandong Zeyu Heavy Industry Science and Technology Co.,Ltd. , https://www.zeyumixer.com